Limited Space for Equipment Shelter Case Study
Fiberglass Protection for Motor Control Center
Amsted Rail, a global leader in manufacturing railroad car undercarriages, including wheels, axles, bearings, and brake systems, is based in Granite City, Illinois. They recently sought to expand their operations but found that space limitations within the plant's existing footprint posed a significant obstacle. They solved their dilemma with an external fiberglass equipment shelter designed and built by Shelter Works.
Sand washing is a critical process in a foundry environment. The sand used in casting must be meticulously cleaned to remove impurities, ensuring the integrity of the molds and, ultimately, the quality of the final cast products. To achieve this, the sand washing process relies on electric motor controls, which manage and power the machinery. Properly housing the motor control center (MCC) protects sensitive equipment from environmental factors and ensures reliable operation.
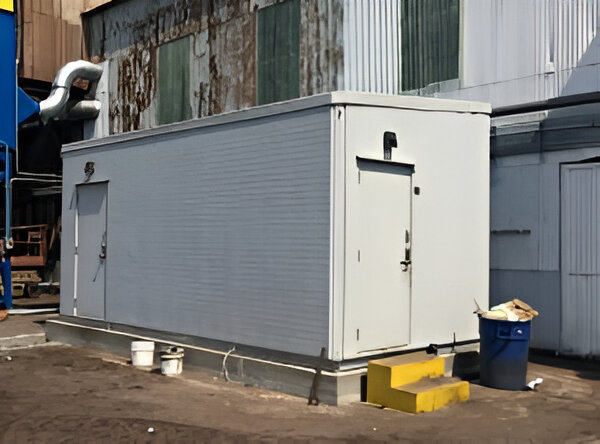
Custom Fiberglass Enclosure
Amsted Rail needed to house the motor control center outside the main foundry building, so it turned to Shelter Works for a custom-engineered solution. The result was a durable, maintenance-free 10 ft by 20 ft by 10 ft fiberglass enclosure that offered the accommodations needed to successfully operate the MCC from an exterior location.
One of the key features of the shelter is its shoebox-style sloped roof. The shelter's placement, within 3 ft of the main building, raised concerns of pooling water between the two structures. The shelter's roof was designed with a 5° slope to route rainwater away from the main foundry building.
The shelter also includes a 12 in by 12 in bulkhead to accommodate conduit runs from the main foundry building to the motor control center. These bulkheads provide a secure, organized entry point for all wiring and connections, crucial for maintaining the integrity and safety of the electrical systems without affecting the shelter's 25 year warranty.
Durability and Stability
The shelter's walls and ceiling were constructed with 2-inch foam insulation, providing excellent thermal protection and energy efficiency. The additional insulation and a 1-1/2 ton wall air conditioner maintain a stable operating environment, safeguarding the motor controls from temperature fluctuations that could otherwise impact performance.
Additionally, the shelter features a fiberglass-reinforced plastic (FRP) encapsulated wood floor covered by durable vinyl tile. This flooring solution enhances the shelter's durability and provides a clean, non-slip surface ideal for the industrial environment. The shelter is also mounted on a steel base skid, which offers a stable and secure foundation for areas with minimal site prep.
Working with Shelter Works
The project team from Amsted Rail visited the Shelter Works' manufacturing facility before finalizing their decision. After seeing the quality and craftsmanship firsthand, they chose the fiberglass shelter over a traditional concrete structure. Mike Sutton of French Gerleman, who was involved in the project, explained, "They did consider constructing a concrete block building, but when they saw how well-made and maintenance-free the Shelter Works fiberglass equipment shelters are, they determined that the Shelter Works building was the most cost-effective option. Plus, the 25-year warranty made this option even more attractive."
Shelter Works delivered the project on time and within budget, meeting all client specifications. The shelter solved the space constraint issue and provided a durable, low-maintenance solution that will protect Amsted Rail's motor control center for years to come.